How are beer coasters made?
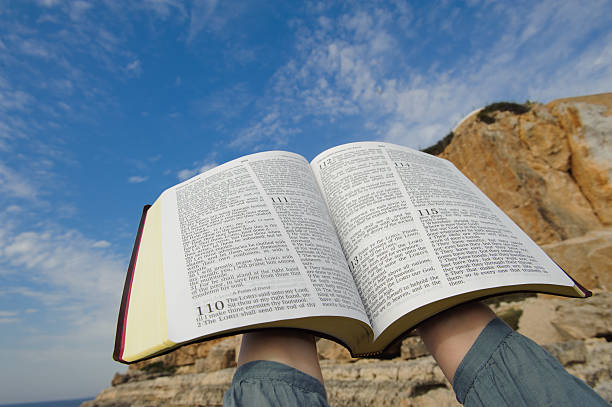
Beer coasters, also known as beer mats, are made through a production process that involves various materials and printing techniques. The specific methods can vary based on the type of coaster, the intended design, and the manufacturing process chosen by the producer. Here is a general overview of how beer coasters are made:
1. Material Selection:
Coasters can be made from a variety of materials, including paper pulp, cardboard, cork, rubber, fabric, or even metal. The choice of material often depends on factors such as cost, absorbency, durability, and the desired aesthetic.
2. Die Cutting:
Once the material is selected, it is die-cut into the desired shape and size. Die cutting involves using a specially shaped cutting tool, called a die, to cut the coaster material into the desired shape, typically a circle or square.
3. Printing:
The design or artwork is then printed onto the coaster surface. Printing methods may include offset printing, digital printing, or screen printing. Offset printing is often used for high-volume production, while digital printing allows for more flexibility in small print runs and intricate designs. Screen printing is a traditional method that can provide vibrant colors and durability.
4. Absorbent Coating (for Paper Coasters):
For absorbent materials like paper pulp or cardboard, a special coating is often applied to enhance moisture absorption. This coating helps prevent condensation from accumulating on the coaster and damaging the surface it is protecting.
5. Additional Features:
Some beer coasters may have additional features added during the manufacturing process. This could include embossing, debossing, foil stamping, or lamination to give the coaster a unique texture or appearance.
6. Cutting and Finishing:
After printing, the coasters are cut into individual pieces. This step ensures that each coaster is a consistent size and shape. The edges may be trimmed or shaped for a polished appearance.
7. Quality Control:
Quality control measures are typically implemented throughout the manufacturing process. This includes checking for color accuracy, print quality, and any defects in the material or printing.
8. Packaging:
The finished beer coasters are then packaged in bulk for distribution. Packaging methods can vary depending on the quantity and the preferences of the manufacturer or client.
Overall, the production of beer coasters involves a combination of material selection, cutting, printing, and finishing processes to create a functional and visually appealing product. The specific techniques used may vary among manufacturers and depend on factors such as budget, production volume, and the desired characteristics of the final coaster.